Tool & mold making
The starting point and the basis for highly precise series production in high quantities is always a perfectly designed, precisely manufactured, long-lasting stamping and/or injection-molding tool.
Optimal conditions for maximum precision
thanks to a state-of-the-art fleet of machinery, as well as air-conditioned manufacturing areas and high cleanliness standards
Fast response time & maximum flexibility
thanks to our technologically fully equipped toolmaking facilities with a high vertical range of manufacture
International structures
allow for efficient and optimally planned processing tailored to customer requirements throughout the entire project process
Quality-centered right from the start
thanks to a state-of-the-art measurement laboratory and the use of highly precise measuring instruments to ensure the quality of individual tool parts, even during their manufacture
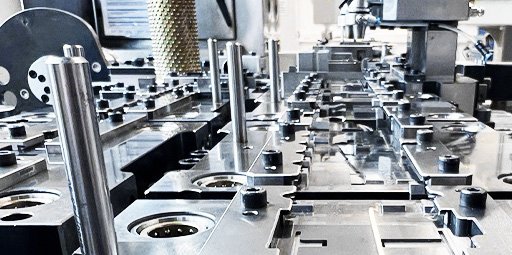
Stamping tools
Depending on the materials, quantities, and product life cycle, our progressive tools combine technologies such as cutting, bending, embossing, deep drawing, laser welding, and resistance welding, allowing for the formation of single-stage production lines. Furthermore, using wire riveting, feeding of individual parts, or additional stamping strips, highly precise assembly processes can be carried out in the tool at high speeds.
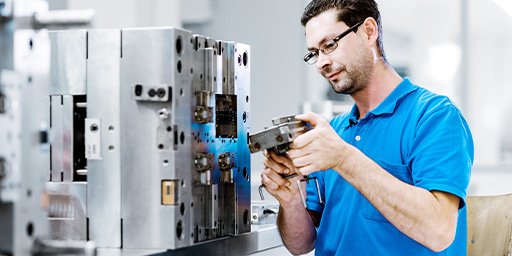
Injection-molding tools
The injection molds for the hybrid technology are of crucial importance for process-reliable production. Our carefully considered, precisely designed injection molds satisfy the high dimensional requirements for plastic-metal composites. This allows us to manufacture products that are perfectly coordinated to customer requirements.
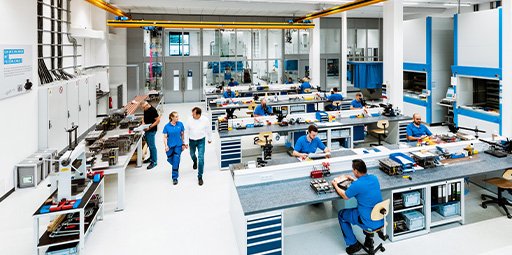
Tool assembly & functional testing
The assembly of the individual tool parts that we manufacture with high precision for series tools is carried out entirely by the team at our toolmaking facilities. Our high-performance tools are then functionally tested under real-world conditions. The technology center specially established for this has fully equipped BRUDERER automatic stamping presses that include laser technology and tandem feeding, as well as state-of-the-art wrapping and measuring technology. This allows us to carry out a comprehensive test and to optimize the stamping process – including integrated laser processes, if desired – already prior to the start of series production.
A multitude of pooled expertise.
Individual manufacturing for tool & mold making.
We have always remained true to our roots, which lie in the manufacturing of high-performance tools. Consequently, company-internal tool development and the continual optimization of series tools and of all the machine tools and systems required for manufacturing, play a central role in our business philosophy. We are therefore able to offer our customers solutions from a single source – from the conception and design of product and process through to the highly skilled manufacturing of corresponding stamping and injection-molding tools. Our technologically diverse, state-of-the-art fleet of machinery combined with our highly qualified team allow for all individual tool parts to be produced entirely in-house. In this way, tool and mold making forms the core and the basis for manufacturing highly precise end products.
Wire EDM
Latest-generation wire EDM machines combined with carefully thought-out premises ensure precise geometries at the highest level. Irrespective of the material hardness, we manufacture with all electrically conductive materials. By using incredibly fine EDM wires, from diameters of 0.33 mm for coarse roughing processes down to 0.02 mm for the finest contours, we can manufacture workpieces with an accuracy of ± 0.001 mm for surface qualities up to Ra 0.06.
Sinker EDM
On our sinker EDM plants, we are able to manufacture very complex, highly precise three-dimensional contours. In such operations, precision takes precedence over everything else: our components are manufactured with a dimensional tolerance of ± 0.003 mm, which can be reduced even further in the case of special requirements. These components are always individually tailored to our customers’ respective requirements. Perfect working conditions allow for manufacturing at a constant temperature and without any draft. We perform a daily calibration via our master reference element as a matter of course.
HSC milling
On our high-quality Röders milling machines, we achieve economic results with maximum precision and surface quality. We work with milling cutters of up to 0.1 mm in diameter, ultra-fine molds on electrodes, and embossing punches. We predominantly use highly accurate milling cutters made from carbide and PCD. Special materials and steel up to 70 HRC can be machined, and we also mill carbide and ceramic with maximum precision. In seamless interaction with wire EDM and continual dimensional testing, we are able to manufacture across shifts using automated processes.
Milling
Many of our components begin undergoing processing in the milling stage. To this end, we have a wide range of machining capabilities in-house: on state-of-the-art CNC five-axis machining centers, we manufacture milled parts for our equipment from a wide range of materials and to the highest level of precision. For this, in addition to a Hermle C32 U, we have a Mikron HPM 1350 U for the horizontal and vertical machining of workpieces.
Flat & profile grinding/
optical grinding
Perfectly manufactured tool and mold components form the basis for efficient and dimensionally accurate series production. At our grinding facility, in addition to flat grinding, we also carry out highly precise optical grinding on CNC plants. This is always done with a focus on maximum precision, surface quality, and productivity. More specifically, we achieve accuracies down to 1 µm and surface qualities down to Ra 0.02.
Laser ablation
Using laser ablation, we can produce complex parts with five-axis machining efficiently and in top quality. The laser technology allows us to manufacture embossing dies and inserts with breathtaking speed and precision. The machining of a wide range of materials consequently opens up new methods of manufacturing for us. Here too, in combination with HSC milling and sinker EDM operations, we have enormous potential with regard to accuracy, surface quality, and cost effectiveness.
After sales: Individual parts & replacement parts for tools
Beyond the series production of highly precise stamped and plastic-metal composite parts, we are also able to assist our customers with the contract manufacturing of individual parts and replacement parts for tools, thanks to our expertise and capabilities in high-performance toolmaking.
Carbide cutting bushes
Our carbide cutting bushes with integrated fall protection are manufactured in KRAMSKI standard dimensions or in accordance with customer drawings. The complete unit is rounded off by the accompanying hole stamp in carbide quality.
Benefits at a glance:
- Made from carbide with integrated fall protection
- Precision and resistance
- Minimization of downtimes
More information can be found in our product flyer.
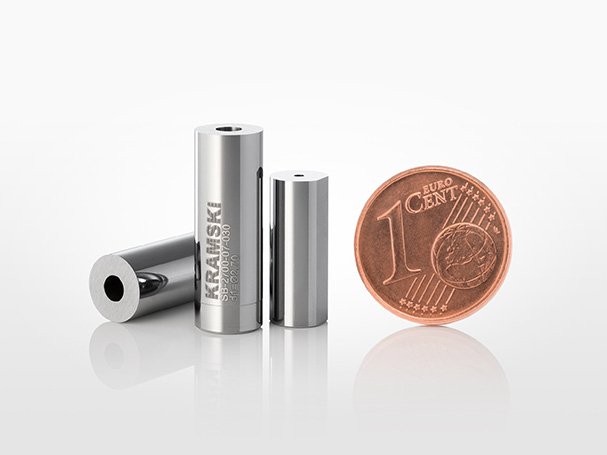
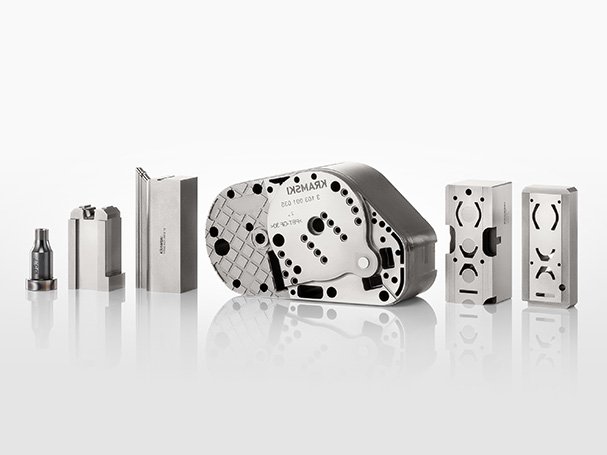
Replacement parts made from carbide &
Special Alloys
Manufacturing on the basis of specific drawings allows us to guarantee 100% replaceability and to provide our customers with the necessary wear parts and replacement parts to the highest level of quality and precision in the shortest possible time. To manufacture our replacement parts, we draw on our entire manufacturing expertise and offer parts that are profile-cut, processed with wire or sinker EDM, and/or HSC-milled. Upon request, we can also provide a corresponding measurement report.
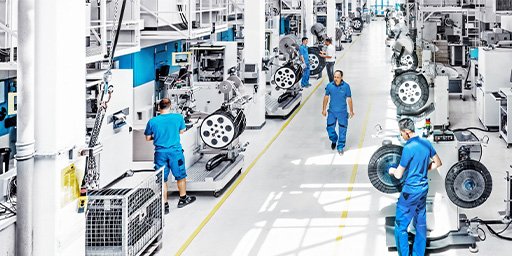
Stamping technology
Our core areas of expertise include the series manufacturing of highly precise stamped parts with the integration of various methods into the stamping process.
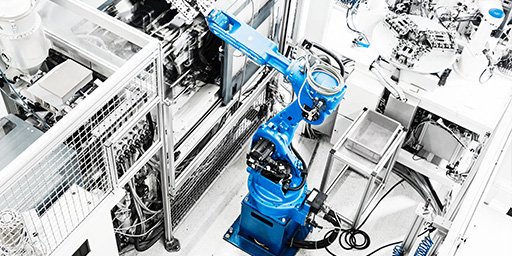
Injection-molding technology
Another of our core areas of expertise lies in combining stamped metal insert parts and plastic in semi- and fully automated series production.